سنگ آهن چیست؟
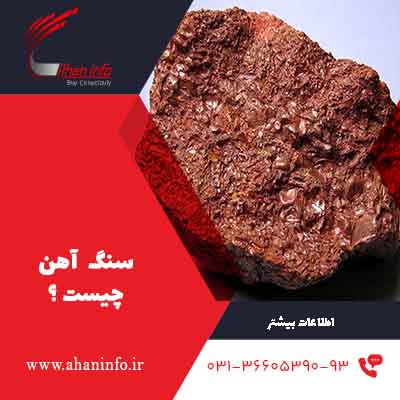
سنگ آهن (Iron ore) یک نوع سنگ معدنی است که در ترکیبات آن آهن (Fe) و دیگر عناصر وجود دارد. سنگ آهن به همین شکل قابلیت استفاده نداشته و باید ناخالصی های آن با استفاده از عملیات های ذوب و احیا، از بین بروند. سنگ آهن یکی از فراوان ترین سنگ های فلزات در زمین به شمار می آید. در واقع حدود 5 درصد از کل پوسته زمین از اکسید آهن تشکیل شده است.
سنگ های پوسته زمین دارای کانی های مختلفی
در ترکیبات خود هستند. دو کانی مهم و رایج در سنگ آهن با نام های هماتیت و مگنتیت
شناخته می شوند. در این بین هماتیت نوعی کانی با فرمول Fe2O4 می باشد که با نام های حدید و شادنه نیز عنوان می شود. این کانی
با استفاده از اسید کلریک و آب تمیز شده و عناصر اصلی درون ترکیبات آن شامل 70
درصد آهن و 30 درصد اکسیژن است و بیشترین کاربرد آن در رنگ سازی و تولید ضد زنگ ها
می باشد. این کانی دانه دانه بوده و قابلیت تغییر رنگ از نقره استیل تا قهوه ای
مایل به قرمز را دارد.
کاربرد
های سنگ آهن
امروزه اشکال متفاوتی از سنگ آهن در بازار
وجود دارد که بیشترین تفاوت آن ها در آنالیز شیمیایی و شکل ظاهری است. اصلی ترین
کاربرد سنگ آهن نیز در تولید ورق آهن و در نتیجه ورق های فولادی است. قیمت ورق آهن نیز برگرفته از نوع استخراج و احیا سنگ آهن متغیر بوده و البته بر نرخ
محصولات نهایی فولادی اثرگذار است.
در واقع می توان گفت فولاد حاصل از احیا سنگ
آهن سبب تولید ورق فولادی سیاه یا آهنی شده که طی انجام عملیات های مختلف بر روی
آن، سایر ورق های فولادی از جمله روغنی، اسیدشویی، گالوانیزه، رنگی و ... به دست
می آیند. کاربرد سنگ آهن نیز به سبب تولید فلز آهن، فولاد، چدن و مقاطع فولادی در
صنایع زیر می باشد:
- خودروسازی :
تجهیزات و ابزارها
- ساخت ابزار و
ادوات جنگی
- تولید فولاد و
ساخت سازه های فولادی
- تولید بتن و
سیمان
- شستشوی ذغال سنگ
و برخی رنگدانه ها
- گل حفاری
- آهن پودرشده:
برای ساخت برخی از فولاد ها، قطعات خودروسازی و کاتالیست ها
- آهن رادیواکتیو
( آهن ۵۹) : به کارگیری در
صنعت داروسازی برای یک عنصر ردیاب در تحقیقات فلزکاری
- اکسید آهن سیاه:
به کارگیری آن برای رنگدانه در ترکیبات پولیش، فلزکاری، داروسازی، ساخت
جوهرهای مغناطیسی و فریت ها (هیدرواکسید آهن) در صنعت الکترونیک
- آهن قرمز: ساخت
جوهر پرینت، نقاشی ها، لوازم آرایشی مانند سایه، رنگ های هنری، کود، پلاستیک
ها و موارد صنعتی
مزایای
سنگ آهن
با این وجود می توان گفت از سنگ آهن، در
تولید فلز آهن، فولاد، مقاطع و ورق های فولادی استفاده می شود. بر اساس اطلاعات و
آمار ها نیز حدود 98 درصد از سنگ آهن استخراج شده از معدن، برای ساخت فولاد و
مقاطع آن به کار برده می شود و موارد ذکر شده در فوق زیر مجموعه این فلزات یا 2
درصد از کاربردهای دیگر سنگ آهن به شمار می آیند. همچنین کی از مهم ترین مزیت های
سنگ آهن، قابلیت بازیافت محصولات نهایی حاصل از آن است.
با یک مثال ساده می توان گفت بسیاری از
تجهیزات زندگی روزمره ما از ورق گالوانیزه فولادی است که ماده اولیه آن سنگ آهن به
شمار می آید. پوشش دهی سقف های داخلی و خارجی، بدنه، لوله بخاری و تجهیزات گرمایشی
و سرمایشی، بدنه لوازم خانگی، بدنه و شاسی خودرو و ... از موارد کاربرد این محصول
هستند.
در واقع فولاد گالوانیزه از طریق اسیدشویی
ورق آهن یا سیاه و روش غوطه ور شدن آن در حوضچه های مذاب حاوی فلز روی تولید می
شود. این محصول به سبب داشتن یک پوشش حفاظت کننده، دارای مقاومت بالایی در برابر
آب، خوردگی، رطوبت و اکسیداسیون می باشد، اما جالب است بدانید خرید ورق گالوانیزه با وجود داشتن این ویژگی ها مقرون به صرفه بوده و
از این رو میزان تقاضا برای آن زیاد است. از سایر مزیت های سنگ آهن که سبب کاربرد
گسترده آن در صنایع شده است، می توان به موارد زیر اشاره کرد:
- استحکام قابل
توجه
- فراوانی منابع و
معادن اولیه
- سهولت در فرآوری
و حذف ناخالصی ها
- آسان بودن مراحل
ذوب
- قیمت مناسب
- تولید آهن خام و
به سبب آن محصولات فولادی
البته بهتر است بدانید سنگ آهنی که برای هر
کدام از کاربری های ذکر شده مورد استفاده قرار می گیرد، باید ترکیبات شیمیایی
مناسبی داشته باشد. میزان آهن در این سنگ های خام مورد استفاده در تولید سایر
فلزات 25 تا 30 درصد است.
نحوه
استخراج سنگ آهن
بهتر است بدانید نحوه استخراج
سنگ آهن که به دو صورت رو باز و زیرزمینی می باشد، بر کیفیت محصول نهایی حاصل از
آن تأثیر به سزایی دارد؛ از این رو در صورتی که معدن مورد نظر، رو بسته یا
زیرزمینی باشد، مراحل زیر برای آن در نظر گرفته می شود. پیش از بررسی این مراحل
نیز بهتر است بدانید علاوه بر کیفیت، قیمت آهن آلات نیز بسته به این موضوع تعیین می
شود؛ زیرا نحوه استخراج و فراوری سنگ آهن است که هزینه تولید یک محصول و همچنین
کیفیت آن را به عنوان مهم ترین ماده اولیه تحت تأثیر قرار می دهد.
حفاری
ابتدایی ترین مرحله در
استخراج سنگ معدنی آهن، حفاری می باشد. از این رو برای انجام این مرحله، باید
چندین چال با یک سری الگو مشخص به وسیله دستگاه های مخصوص در این زمینه صورت گیرد.
سپس درون این چاله ها، با مواد منفجره مخصوص پر می شود.
انفجار
در این مرحله با تخلیه کامل مواد منفجره
داخل چاله ها، کارگران باید در یک محل ایمنی که جان پناه نام دارد، قرار بگیرند تا
عملیات انفجار صورت گیرد. این عملیات سبب خرد شدن سنگ ها خواهد شد و مهم ترین ماده
منفجره مورد استفاده در این فرآیند، سوخت آمونیوم نیترات (Ammonium Nitrate Fuel
Oil) یا آنفو نامیده می شود.
بارگیری
سپس باید بارگیری سنگ های خرد شده به وسیله
ابزار آلات و دستگاه های مخصوص انجام گیرد. این عملیات ها به طور معمول با استفاده
از ترکیب شاول و کامیون صورت گرفته؛ به طوری که شاول سبب برداشتن سنگ های خرد شده
از روی زمین شده تا آن ها را داخل مخزن کامیون بریزد. همچنین باید ظرفیتی که شاول
های معمولی دارند در حدود 375/0 تا 5 متر مکعب یعنی 2 تا 25 تن می باشد؛ در صورتی
که این ظرفیت برای مدل های قوی و بزرگ در حدود 29 متر مکعب یعنی 145 تن است.
باربری
در نهایت به آخرین مرحله در استخراج سنگ آهن
می رسیم که باربری نام دارد. در این بخش باید کامیون یا در اصطلاح دامپرتراک، خرده
های سنگ آهن را بسته به این که با چه خلوصی همراه هستند، به کارخانجات فولاد سازی
و فراوری در نظر گرفته شده منتقل کند. این کامیون ها نیز ظرفیت های مختلفی دارند؛
از این رو برای معادن آهنی بزرگ یا متوسط به طور معمول از تراک هایی در ظرفیت 35
تن استفاده می شود.
مراحل
فرآوری سنگ آهن
فرآوری سنگ آهن شامل مراحل مختلف و بسیار مهمی می باشد که در این قسمت به بررسی این مراحل خواهیم پرداخت:
غربالگری
پس از اتمام مراحل استخراج
سنگ آهن، خرده های سنگ آهن را از آلودگی ها و ناخالصی ها جدا می کنند که به این
عملیات غربالگری گفته می شود. فرآوری این سنگ
نیازمند انجام فرآیند های فیزیکی و شیمیایی ویژه است. برای انجام فرآیند شیمیایی،
باید سنگ های اکسیدی آهن با استفاده از کربن احیا شده تا عنصر آهن آزاد شود.
سپس جهت خالص سازی، سنگ آهن طی مراحل خرد
کردن، آسیاب کردن، سرند کردن، شستشو استفاده از جدا کننده مغناطیسی یا به روش
فلوتاسیون تغلیظ می شود. در این روش ها، عیار سنگ آهن تا حدود 60-65 درصد بیشتر می
شود
تولید سنگ آهن دانه بندی شده
سپس باید آن ها را در اندازه های 6 تا 25
میلی متری برای قرار دادن در کوره در آورند. این عملیات ها به خصوص برای تولید سنگ
آهن دانه بندی شده تحت فرآیند های ذوب و احیا در کوره ها و به روش امروزی انجام می
گیرد. روش کوره بلند یکی از بهترین روش های جداسازی آهن از ترکیبات سنگ آهن بوده
که پودر آهن حاصل از آن تیره رنگ رو به قهوه ای می باشد.
در کوره های وزشی، سنگ آهن تغلیظ شده را به
همراه مواد افزودنی مانند سنگ آهک، زغال و کک در دمای بالا قرار داده تا فلز با استفاده
از این حرارت و جریان گازهای حاصل از سوخت مواد افزودنی، ذوب شود. در نهایت آهن
مذاب و تفاله ناخالصی های سنگ آهن نیز به تدریج از کوره تخلیه می شوند.
تولید کنستانتره
بهتر است بدانید تولید یک تن آهن در یک کوره
بلند، نیازمند 75.1 تن سنگ آهن، 750 کیلو زغال سنگ و 250 کیلو سنگ آهک است. همچنین
دمای هوا در مرکز کوره 1600 درجه سانتی گراد است. تمامی این عوامل به همراه کیفیت
سنگ آهن استخراجی در نرخ روز آهن مورد نیاز برای تولید سایر آلیاژ ها تأثیر دارد.
البته می توان از روش های دیگر مانند میدرکس یا کوره های القایی نیز استفاده کرد. با این وجود ابتدایی ترین ماده پس از سنگ آهن دانه بندی شده، کنستانتره است این مواد با یک دیگر ترکیب شده تا با فرآوری سنگ آهن، اکسیژن آن آزاد شود و به این ترتیب کنستانتره، گندله، آهن اسفنجی و سپس فولاد خام به دست آیند.
مشخصات سنگ آهن
همان طور که می دانید سنگ آهن
به عنوان یکی از مهم ترین سنگ های معدنی، حدود 5 درصد از جهان را فراگرفته است.
این ماده دارای کانی های مختلفی می باشد. نام کانی مگنتیت نیز برگرفته از یک واژه یونانی و به معنای آهن ربا می
باشد. فرمول شیمیایی مگنتیت Fe3O4 است و
در ترکیبات آن حدود 72 درصد آهن به همراه سایر عناصر وجود دارد. مگنتیت رنگی مایل
به سیاه داشته و خاصیت مغناطیسی دارد.
لازم به ذکر است سنگ آهن تنها با کانی های
نام برده شده یافت نمی شود و این سنگ در پوسته زمین انواع مختلفی را همراه با کانی
های متنوع دارد؛ در نتیجه با نام آن کانی ها نیز شناخته می شود. برخی از این سنگ آهن ها شامل زئولیت، لیمونیت، سیدریت، گرینالیت، مارکالیت
و ... هستند.
مهم ترین نکته برای به دست آوردن سنگ آهن،
پیدا کردن معادن غنی این سنگ است که توسط کارشناسان حرفه ای معادن انجام می گیرد.
پس از شناسایی، سنگ آهن را استخراج کرده و ناخالصی های آن را جدا می کنند تا آهن
خالص به دست آید. آهن به دست آمده از سنگ آهن به صورت پودری
بوده و رنگی تیره دارد.
این ماده در برابر اکسایش و ضربه بسیار آسیب
پذیر است و باید همراه با عناصر دیگر ترکیب شود. به ترکیبات آهن با سایر عناصر
شیمیایی مانند نیکل، کربن و کروم، آلیاژ گفته می شود. دو نوع از مهم ترین آلیاژهای
آهن، فولاد و چدن هستند که حاصل آن ها مقاطع و ورق های فولادی با خواص متفاوت و
کاربری های متنوع هستند. از آن سنگ قوی و سخت پس از فرآیندهای مختلف، ورق های
فولادی رنگی به دست می آیند. در واقع قیمت روز ورق رنگی بسته به کیفیت سنگ آهن
اولیه و نرخ آن، هزینه های تولید و حمل و نقل برمی گردد.
انواع
سنگ آهن
سنگ آهن از نظر شکل ظاهری و کانی به انواع
مختلفی تقسیم بندی می شود:
از نظر ظاهری
شکل ظاهری: دانه بندی شده، گندله، کلوخه و
کنسانتره
گندله
گندله از نرمه سنگ آهن و سایر مواد افزودنی
تولید شده و ظاهری شبیه به گلوله دارد. این گلوله در ابتدا خام بوده و طی مراحل
مختلف سخت و پخته می شود. برای استفاده از گندله و تولید آهن خام روش احیا مستقیم
یا کوره بلند استفاده می گردد.
دانه بندی
روش تولید سنگ آهن دانه بندی شده به صورت بدون
آب و خشک می باشد و این کانی دارای عیار پایینی است؛ از این رو برای استفاده در
کوره احیا مناسب نیست و خاصیت احیا پذیری پایین سبب شده تا از آن کمتر استفاده
شود.
کلوخه
یکی از رایج ترین انواع سنگ آهن از نظر شکل
ظاهری، کلوخه نامیده می شود و به صورت سالانه صدها میلیون تن از آن تولید شده و به
کار برده می شود.
کنستانتره
بر خلاف سنگ آهن دانه بندی شده، کنسانتره به
وسیله آب تولید شده و فرآوری آن شامل مراحلی مانند خرد کردن، آسیاب کردن، پرعیار
سازی و آبگیری است. عیار مناسب کنسانتره سبب استفاده از آن در مصارف مختلف و قابل
بهره برداری شده است.
از نظر کانی
نوع کانی: شامل هماتیت، مگنتیت، زئولیت،
لیمونیت، سیدریت که رایج ترین آن ها یعنی هماتیت و مگنتیت شرح داده شد.
هماتیت
یکی از ابتدایی ترین مواد
معدنی یا در واقع کانی هایی که در ترکیبات سنگ آهن یافت می شود، هماتیت نامیده شده
و رنگی سیاه و سفید دارد. از مهم ترین مشخصات کانی هماتیت می توان به غیر مغناطیسی
بودن آن اشاره کرد؛ از این رو تغییر رنگ این ماده از نقره ای تا قهوه ای امکان
پذیر می باشد و حدود 6/69 درصد از آن آهن می باشد.
مگنتیت
دومین کانی که در بخش مشخصات
سنگ آهن نیز اشاراتی به آن کردیم، مگنتیت با رنگ سیاه و سفید می باشد. این کانی
دارای یک حالت مغناطیسی بوده و آهن آن نیز در حدود 72/4 درصد است. البته بهتر است
بدانید ناخالصی های موجود در این کانی سبب کاهش عیار آن خواهند شد.
لیمونیت
لیمونیت یکی دیگر از ماده های
معدنی درون سنگ آهن به شمار می آید و نام آن از کلمه یونانی limus گرفته
شده که به معنای گل و لجن است. در واقع این نوع کانی ترکیبی از هیدروکسیدها و
اکسیدهای آهنی است؛ از این رو تنها جایی که می توان آن را پیدا کرد، در اکسیدان به
همراه ژیزمان های گوتیتی می باشد.
سیدریت
و در نهایت سیدریت نیز یکی
دیگر از کانی های کمیاب سنگ آهن بوده و نام آن برگرفته از کلمه یونانی Sideros می
باشد. این کلمه به معنی سنگ معدن آهنی مناسب است.
بزرگرین
معادن سنگ آهن در جهان
با توجه به افزایش استفاده از
فولاد و محصولات فولادی حتی در زندگی روزمره بشر، می توان به اهمیت استفاده از سنگ
آهن پی برد. این ماده توسط معادن طبیعی زمین به دست می آید و با توجه به این که
همواره با کمبود مواد اولیه ای مانند قراضه آهن، مواجه هستیم، می توان گفت استخراج
سنگ آهن روز به روز بیشتر خواهد شد. از این رو باید گفت بزرگ معادن سنگ آهن در
جهان شامل موارد زیر هستند:
- واله سامارکو برزیل با ظرفیت تولید سالیانه 450 میلیون تن
- همرسلی استرالیا با ظرفیت تولید سالیانه 400 میلیون تن
- کاراجاس برزیل با ظرفیت 300 میلیون تن
- سیشن آفریقای جنوبی همراه با ظرفیت 250 میلیون تن
- کیرونا سوئد با ظرفیت 200 میلیون تن
- موردیتیا برزیل با ظرفیت 320 میلیون تن
- رویبرد استرالیا همراه با ظرفیت 290 میلیون تن
- بونگ لیبریا با میزان استخراج 240 میلیون تن سالیانه
- کورومبا برزیل در میزان استخراج 195 میلیون تن
- گراند رپیدز کانادا با استخراج سالیانه 150 میلیون تن
عوامل
موثر بر قیمت سنگ آهن
از مهم ترین عواملی که نرخ
سنگ آهن و در نتیجه محصولات حاصل از آن را تحت تأثیر قرار می دهند، می توان به
نحوه استخراج، ظرفیت معدن، میزان خلوص سنگ آهن، نوع کانی موجود در آن، روش استخراج
و چالش های موجود در آن، ماشین آلات صنعتی مورد استفاده، ظرفیت کامیون، نوع جاده و
هزینه حمل و نقل اشاره داشت.
هر چه سنگ آهن از خلوص بیشتری
برخوردار باشد، میزان استفاده از آن نیز به خصوص برای تولید گندله و آهن اسفنجی به
عنوان دو ماده اولیه تولید فولاد بالاتر خواهد رفت.
جمع
بندی
در این مطلب به مصارف گسترده سنگ آهن، انواع و نوع فرآوری آن پرداخته شد. با این وجود می توان گفت سنگ آهن کاربرد بسیار گسترده را در صنایع و زندگی روزمره هر یک از ما دارد، اما با وجود فراوانی منابع سنگ آهن، باید در مصرف آن دقت کرد. پیشنهاد می شود تا حد امکان برای ساخت فولاد از قراضه های آهنی به جای سنگ آهن استفاده کرد. کشورهای چین، استرالیا و برزیل بزرگ ترین تولید کنندگان سنگ آهن در جهان به شمار می آیند.