کلوخه سازی چیست؟
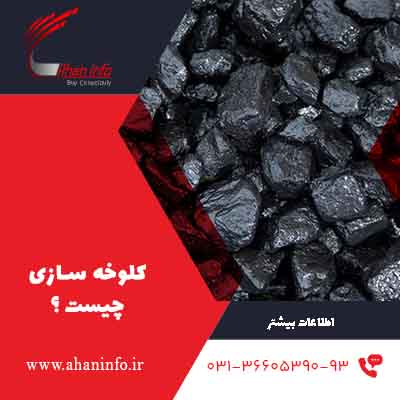
همان طور که می دانید فرآیند تولید آهن و فولاد نیاز به استخراج سنگ های معدنی آهن دارد، اما این سنگ معدنی خلوص بالایی نداشته و باید فراوری یا احیا گردد تا ناخالصی های آن جدا شده و در نهایت فولاد خام به دست آید. برای انجام این فرآیند نیز سه روش وجود دارد که به ترتیب رواج در جهان به وسیله کوره بلند، کوره های میدرکس و کوره های القایی انجام می گیرد. حدود 60 درصد از فولاد جهان به روش کوره بلند تولید می شود، اما در کشور ما به علت داشتن منابع غنی گاز، از روش میدرکس که بر پایه کوره های قوس الکتریکی انجام می گیرد، استفاده می کنند.
با این وجود برای
استفاده از هر کدام این روش ها، سنگ معدنی با شکل اولیه خود کاربردی نداشته و باید
به قطعات کوچک تر و خردتر تبدیل شود. پس از خرد شدن سنگ آهن، کنسانتره آهن تولید
می شود و پس از فرآیند های مختلف نیز به کلوخه و گندله تبدیل می گردد. این محصولات
مصارف بسیار زیادی را در واحدهای فولادسازی جهان به خود اختصاص می دهند.
فرآیند کلوخه سازی نیز نوعی عملیات حرارتی است که در دسته فرآیندهای آگلومراسیون قرار می گیرد و به نوعی انجام می شود که سبب خرد شدن مواد خام اولیه با سایز کوچک به قطعاتی به نام کلوخه تبدیل می گردند. در واقع می توان گفت در جهت ذوب و تصفیه ذرات ریز و خاکه های سنگ آهن، فرآیند کلوخه سازی صورت می گیرد. برای انجام آن نیز خاکه های سنگ معدنی آهن به همراه قطعات کوچک و آهک، آگلومره برگشتی و افزودنیهای مختلف در اندازه های مشخص را با یک دیگر مخلوط می کنند. پس از ترکیب شدن مواد آن ها برای گرما دهی به دستگاه کلوخه سازی انتقال داده و سپس حرارت سبب ساخت کلوخه خواهد شد.
ویژگی های کلوخه
با این وجود می توان گفت کلوخه یکی از محصولات مهم در فراوری سنگ آهن و تولید فولاد به شمار می آید که باید از ویژگی های مشخصی برخوردار باشد. ابتدا بهتر است بدانید کلوخه باید در سایز های مناسبی وارد کوره آهن سازی گردد. از دیگر مشخصات این مواد نیز می توان به استاندارد بودن مقاومت مکانیکی و شیمیایی، سطح کیفیتی بسیار بالا و ترکیب درست مواد اشاره کرد. لازم به ذکر است اگر از کلوخه های با کیفیت در ساخت فولاد استفاده شود، سبب افزایش بازدهی و مقاومت در آن خواهند شد.
تفاوت کلوخه با گندله
در مورد تفاوت کلوخه با
گندله ابتدا بهتر است بدانید کلوخه به همراه مواد اولیه خام سنگ معدنی به صورت
متراکم تولید می شود و از نظر مقاومت مکانیکی، شیمیایی و دمایی کاملاً استاندارد
تولید می شود که برای استفاده در کوره نیز مناسب است. این در صورتی است که برای
تولید گندله از مواد بازیافتی استفاده نمی کنند. مواد اولیه برای تولید گندله شامل
آهک، کنسانتره آهن، بنتونیت، کک و ... می باشند که قطعا باید با کنسانتره آهن
ترکیب شوند.
گندله ها نیز در جهت
استفاده در کوره های احیا باید تحت حرارت قرار بگیرند. ابعاد این مواد نیز حداکثر
گلوله های 16 میلی متری می باشند و هر چه سایز آن از اندازه مشخصی کمتر یا بیشتر
باشد، مجدد بازیافت شده و وارد چرخه تولید می شوند. پس تفاوت گندله و کلوخه در روش
تولید و شرایط کلی آن ها می باشد، اما هر دو در فولاد سازی مورد استفاده قرار می
گیرند.
همچنین دیگر تفاوت این دو ماده در مواد اولیه مورد استفاده برای تولید می باشد. مواد اولیه برای تولید یک گندله با کیفیت و مناسب بیشتر از تولید کلوخه هستند، در صورتی که کلوخه در واقع به وسیله خاکه های سنگ آهن با ترکیب سایر افزودنی ها به دست می آید.
برای اطلاع از قیمت ورق اسیدشویی فولادمبارکه به دسته بندی مربوطه مراجعه نمائید.
جمع بندی
کلوخه سازی یکی از انواع
عملیات های آگلومراسیون حرارتی به شمار می آید که در فولادسازی مورد استفاده قرار
می گیرد. در واقع کلوخه یکی از مهم ترین مواد اولیه در تولید فولاد مذاب شناخته
شده و از سنگ آهن خام که از معادن استخراج می شود، به دست می آید. در واقع برای
ذوب و تصفیه ذرات کوچک و قطعات ریز سنگ آهن، آن ها را به همراه یک سری افزودنی دیگر
مانند آهک، با یک دیگر ترکیب کرده و سپس در کوره حرارت می دهند.
نسبت این مواد برای
ترکیب با یک دیگر باید کنترل شده و مناسب باشد تا کلوخه در مرحله آگلومره کیفیت
بالایی داشته باشد. در نهایت می توان گفت کلوخه و گندله دو ماده اصلی در فرآیند
فولادسازی به شمار می آیند و در فرآیند احیا سنگ آهن که سه روش اصلی دارد، از آن
ها استفاده می کنند تا آهن جامد و سپس فولاد مذاب به دست آیند. فولاد مذاب نیز با
ترکیب شیمیایی تنظیم شده به وسیله پاتیل های حمل مذاب به واحد ریخته گری منتقل شده
تا شمش های منجمد و سپس اسلب فولادی جهت تولید محصولات فولادی تولید شوند.