فولاد مارتنزیت چیست؟ کاربرد و مزایای آن
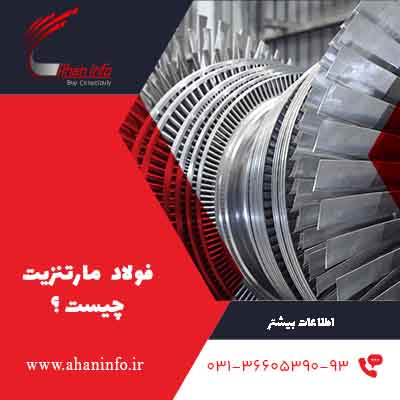
فولاد مارتنزیت ممکن اسم نسبتاً سخت و
ناآشنایی داشته باشد، اما در زندگی روزمره ما به راحتی یافت می شود. تا به حال به
ساختار چاقوهای آشپزخانه یا ابزارهای مختلف بسیار برنده دقت کرده اید؟ این محصولات
به صورت مداوم با اجسام یا ابزار آلات دیگر در ارتباط و سایش قرار دارند، اما
استحکام آن ها ثابت است و موارد بسیار کمی از تغییرات آن ها وجود دارد.
فولادهایی که برای ساخت این گونه محصولات و
ابزارآلات مورد استفاده قرار می گیرند، مارتنزیت نام دارد که در ادامه به بررسی
ساختار، تفاوت با سایر فولاد ها، مشخصات، کاربرد و روند تولید آن می پردازیم. بهتر
است بدانید مارتنزیت در واقع یک ساختار فولادی می باشد که به وسیله جا به جایی
تعداد بسیاری از اتم ها به شکل گروهی و همزمان ایجاد می گردد.
در واقع این ساختار از فولادهای ضد زنگ
تولید می شود که به پنج دسته اصلی فریتی، آستنیتی، مارتنزیتی، رسوب سخت شونده و
داپلکس تقسیم بندی می شوند و تنها بر روی فولادهایی قابل انجام است که بیشتر از
3/0 درصد کربن در ساختار خود داشته باشند. در آلیاژهای فولادی، آهن و کربن ماتنزیت
از طریق سرد شدن آستنیت به دست می آید که فرآیندی کاملاً مستقل از نفوذ می باشد.
در واقع میکرو ساختار مارتنزیتی، سخت ترین ساختاری است که در یک فولاد رخ می دهد.
استحاله مارتنزیتی
فولادهای مارتنزیتی با استفاده از روش های
عملیات حرارتی، سخت و تمپر خواهند شد و به طور عادی از کوئنچ کردن فولاد در ناحیه
آستنیتی به دست می آیند. در واقع این موضوع که ساختار آستنیتی به سرعت سرد می گردد
و همچنین اتم ها به شکل گروهی حرکت می کنند، سبب به وجود آمدن استحاله مارتنزیتی و
فولاد مارتنزیت خواهد شد. این نوع فولادها می توانند از فولاد پرکربن یا کم کربن
با درصد 2/1 تا 3/0 باشند و بدون هیچ نفوذ و بدون برش می باشند.
سرعت سرد شدن این فولادها بسیار بالا می
باشد؛ از این رو سختی و استحکام آن ها نیز زیاد است. از سوی دیگر این سختی سبب
کاربردهای بیشتر فولاد ماتنزیت شده است. این سختی و استحکام نیز به سبب واپیچیدگی
شبکه کریستالی و تنش های داخلی نیز هستند. بیشترین کاربرد این فولادها نیز در
مصارفی است که نیاز به مقاومت در برابر خستگی و سایش باشد. این در صورتی است که
بیشترین سختی فولادهای پرلیتی حدود 400 برینل می باشد، اما فولاد ماتنزیت حدود 700
برینل سختی را به خود اختصاص داده است.
همچنین باید گفت این ساختار در محدوده دمایی 200 تا 320 درجه سانتی گراد به وجود خواهد آمد و در فازهای پرلیت و مارتنزیت نیز، ساختار بینیت به وجود خواهد آمد. ناپایدار بودن مارتنزیت نیز سبب می شود تا عملیات حرارتی تمپرینگ بر روی آن صورت گرفته و سبب تولید محصول زیر گردد.
برای اطلاع از قیمت ورق گالوانیزه کیلویی به دسته بندی مربوطه مراجعه نمائید.
مارتنزیت تمپر شده
همان طور که اشاره شد، عملیات
حرارتی به نام تمپرینگ سبب ایجاد فولاد مارتنزیت خواهد شد. از این رو می توان گفت مارتنزیت تمپر شده یک نوع ریزساختار فولاد است که
در اثر عملیات حرارتی تمپر کردن بر روی مارتنزیت ایجاد میشود. تمپر کردن یک
عملیات حرارتی است که در آن فولاد پس از کوئنچ کردن، به دمای پایینتری (معمولاً
زیر 500 درجه سانتیگراد) گرم میشود و سپس در آن دما نگه داشته میشود.
همچنین در طی این عملیات، اتم
های کربن و صفحات آن ها در مارتنزیت به شکل تدریجی با یک دیگر ترکیب شده تا یک
ساختار کریستالی با دانه های ریزتر به وجود آورند. این عملیات سبب ایجاد انعطاف
پذیری بیشتر در فولادهای مارتنزیت خواهد شد و از سختی آن ها نیز می کاهد. همچنین
مارتنزیت های تمپر شده بیشتر برای تولید فولاد ضد زنگ، ساختمانی و ابزار استفاده
می شوند.
انواع
استحاله مارتنزیت
در فولادهای پرکربن که سختی بسیار بیشتری
دارند، ماتنزیت به سه صورت لایه ای، بشقابی و مختلط به وجود می آید که بر اساس
میکروساختار و تیغه های ماتنزیتی می باشد. در ادامه به شرح اختصاری هر کدام از استحاله های
مارتنزیتی پرداخته ایم:
لایه ای
نوع لایه ای، از قرار گرفتن لایه های
مارتنزیت به صورت دسته ای و در طرف های مختلف به دست می آید که در فولادهایی با
کربن کمتر در حدود 3/0 تا 6/0 درصد به وجود می آید. ریز ساختار این فولادهای
مارتنزیتی نیز شامل لایه های موازی بوده که در اطراف دانه های آستنیت اولیه قرار
می گیرند. این نواحی با نام بسته مارتنزیتی شهرت یافته و هر چه درصد کربن محصول
کمتر باشد، تعداد آن ها بیشتر و لایه ها کمتر خواهند شد.
بشقابی
بر خلاف نوع لایه ای،
مارتنزیت بشقابی در فولادهایی که درصد کربن آن ها بیش از 1 درصد می باشد، به وجود
می آیند. میکروساختار این ماتنزیت نیز شامل تیغه های درشت و سوزنی شکل می باشد.
فولادهای پر کربن از این قبیل، تیغه های مارتنزیت بر روی صفحه های رابط مختلف، به
وجود آمده و سپس تیغه های جدید در استحاله بر روی آن ها تشکیل می شوند؛ به همین
علت ساختار مارتنزیت های بشقابی با میکروسکوپ به شکل نامنظم و به هم ریخته است.
مخلوط
حالت میانی یا مخلوط میان فولادهای
مارتنزیتی لایه ای و بشقابی نیز زمانی اتفاق می افتد که درصد کربن فولاد بین 6/0
تا 1 درصد باشد و به آن ماتنزیت مخلوط می گویند.
برای اطلاع از قیمت ورق روغنی در تهران به دسته بندی مربوطه مراجعه نمائید.
کاربرد
فولاد مارتنزیتی
ویژگی هایی مانند مقاومت و استحکام فولاد
مارتنزیتی در برابر سایش و سختی بالا سبب شده تا از آن برای ساخت ابزارهای تیز و
برنده مانند چاقو، قیچی، میله و ... استفاده کنند. از سوی دیگر می توان به وسیله
اضافه کردن عنصر کرون در حدود 12 تا 18 درصد به فولاد، میزان مقاومت آن را در
برابر خوردگی افزایش داد. فولادهای ضد زنگ مارتنزیتی نیز به همین روش و با افزودن
کروم به ترکیبات آن ها تولید شده و در موارد زیر به کار برده می شوند:
- پره های توربین
- تیغه های ریش
تراش
- چاقوهای
آشپزخانه
- ابزار جراحی
- لوله تفنگ و ...
با این حال بهتر است بدانید یکی دیگر از مهم
ترین کاربردهای قطعات مارتنزیتی در ساخت فولادهای خود سخت شونده یا Hadfield می باشد. البته درست است که ساختار ابتدایی این
فولادها آستینیتی می باشد که به علت وجود عنصر آلیاژی منگنز در ساختار آن است، اما
ساختار آن ها به گونه ای است که با ایجاد کردن کوچک ترین تغییر پلاستیکی، به فولاد
مارتنزیت و سخت تبدیل می شود.
برای اطلاع از قیمت ورق برش خورده به دسته بندی مربوطه مراجعه نمائید.
چه نوع
فولادی برای ساختار مارتنزیت مناسب است؟
یکی از مهم ترین خاصیت هایی
که در فولادهای مارتنزیتی وجود دارد، مربوط به سختی پذیری فولاد می باشد. در واقع
تمامی فولادها را نمی توان به راحتی با سرد کردن سریع به مارتنزیتی و سخت تبدیل
کرد. منظور از سختی پذیری، میزان قابلیت تشکیل شدن مارتنزیت در فولاد به وسیله سرد
شدن سریع ناحیه آستنیت می باشد و با استفاده از نمودارهای TTT و CCT توجیه می گردد.
حال بر اساس این نمودارها،
سرعت سرد شدن فولادها باید به گونه ای باشد که نمودار سرد شدن از ناحیه دمای شروع
و پایان مارتنزیت که خطوط Ms و Mf نامیده می شوند، کاملاً عبور کند. این موضوع باید بدون وارد شدن نمودار در
منطقه تشکیل بینیت و پرلیت رخ دهد؛ در غیر این صورت مارتنزیت در ساختار به وجود
نمی آید و در نتیجه سختی مد نظر تشکیل نمی شود.
با توجه به این ساختار بهتر است بدانید هر
چه میزان آستنیت باقی مانده در ساختار نهایی افزایش یابد، استحکام مارتنزیت نیز
کمتر می شود. یک سری پارامتر نیز بر سختی پذیری فولادها مؤثر هستند که از جمله آن
ها می توان به درصد کربن، ناخالصی ها، سرعت سرد شدن، ضخامت قطعه و عناصر آلیاژی
اشاره کرد و بیشتر بر روی فولادهای کربنی با درصد 3/0 انجام می گیرد؛
زیرا عنصر آلیاژی کربن مهم ترین نقش را در میزان سختی فولاد ایفا می کند.
همچنین اگر سرعت سرد شدن فولاد از یک میزان
خاصی کمتر باشد، فاز پرلیت از نواحی مرزدانه جوانه زده و در نهایت ساختار فولاد از
پرلیت و مارتنزیت به صورت ترکیبی تشکیل می شود که قابل قبول نیست. جالب است بدانید
اگر مارتنزیت کردن فولاد برای قطعاتی که درصد کربن آن ها کمتر از 3/0 می باشد،
انجام شود، به علت کم بودن درصد کربن یک مارتنزیت ناقص و همراه با سختی پایین و
نامطلوب به وجود می آید. در اصطلاح این قطعات را با عنوان فولادهایی که آب نمی
گیرند، می شناسند.
برای خرید ورق رنگی فولاد مبارکه به دسته بندی مربوطه مراجعه نمائید.
برای خرید ورق رنگی فولاد مبارکه به دسته بندی مربوطه مراجعه نمائید.
جمع بندی
در نهایت بهتر است بدانید فرآیند تولید
فولاد مارتنزیت تنها به سرعت بالای سرد شدن ختم نمی شود و برای جلوگیری از شکننده
شدن فولاد، با استفاده از یک عملیات حرارتی در زیر دمای آستنیته تنش های پسماند
داخلی آزاد خواهند شد. از سوی دیگر بخش اضافی کربن که در ساختار BCT فولاد باقی مانده بود، آزاد شده و فازهای تعادلی فریت و سمنتیت به وجود می
آیند.
به این فولاد، مارتنزیت تمپر شده گفته می شود و دارای سختی و استحکام بالا، انعطاف پذیری و همچنین چکش خواری مناسبی است. همچنین این فولادها خاصیت جوش پذیری نسبتاً ضعیفی داشته و برای جلوگیری از آسیب رسیدن به آن، باید پیش از عملیات جوشکاری در دمای 200 تا 400 درجه سانتی گراد پیشگرم شود.