تفاوت ورق گالوانیزه سرد و گرم چیست؟
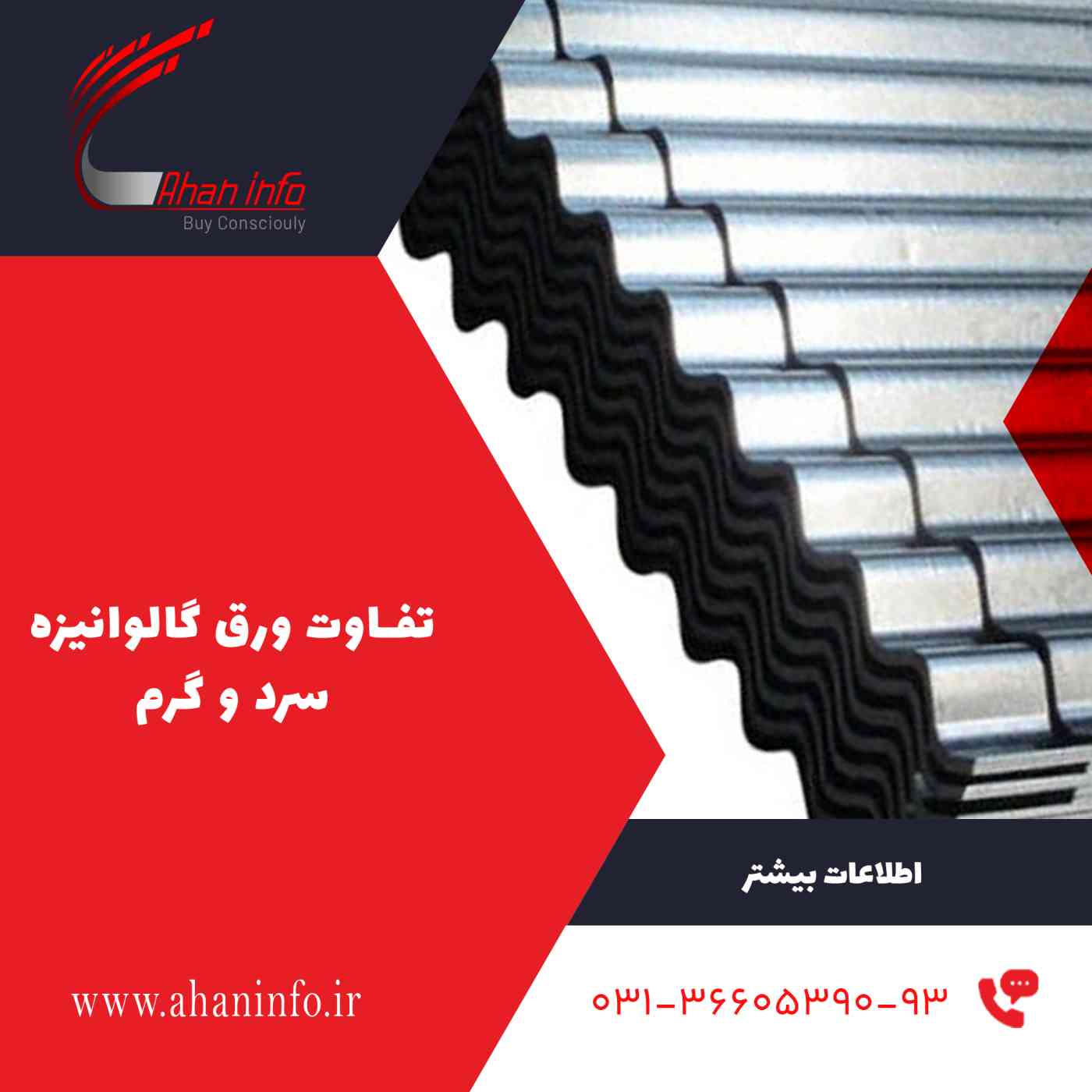
یکی از محبوب ترین محصولات فولادی در صنعت آهن آلات که علاوه بر داشتن کیفیت ظاهری بالا، از مقاومت ویژه ای در مقابل عوامل تهدید کننده فولاد برخوردار است، ورق گالوانیزه نامیده می شود. در این مطلب به بررسی تفاوت ظاهری گالوانیزه گرم و سرد و درونی پرداخته ایم تا درک بهتری از فرآیند تولید این محصولات داشته باشید.
به طور کلی ورق یا کلاف
گالوانیزه از کلاف های فولادی به دست می آیند و طی فرایند نورد گرم که بر روی آن
ها انجام می شود، تولید خواهند شد. پس از این مرحله ورق ها روی اندود می شوند؛ به
عبارتی در مخازن حاوی روی قرار می گیرند. مزیت مهمی که ورق گالوانیزه به نسبت سایر
کلاف های فولادی دارد، در سرسختی آن ها در برابر زنگ زدگی و خوردگی می باشد. همین
نکته مثبت باعث شده تا این فلزات سر سخت در صنایع مختلف کاربرد داشته باشند و همچنین
عمر مفید آن ها به بیش از 50 سال می رسد.
در نتیجه گالوانیزه کردن
یا گالوانیزاسیون فلزات فولاد و آهن طی فرآیند آبکاری سرد و گرم و اعمال شدن پوشش
فلزی بر روی آن ها انجام می شود. آهن و فولاد دو ماده حذف نشدنی از صنایع مختلف
هستند، اما برای جلوگیری از معایبی مانند خوردگی و زنگ زدگی آن ها را گالوانیزه می
کنند. گالوانیزه کردن فلزات به دو روش انجام می شود که در ادامه با بررسی هر روش
درک بهتری از تفاوت گالوانیزه گرم و سرد پیدا خواهید کرد. در واقع اولین تفاوت این
دو در روش تولید آن ها است.
بررسی تفاوت گالوانیزه گرم و سرد از
جنبه تخصصی
به طور کلی غوطه وری
فولاد و آهن در حمام مذاب فلز روی را که مقاومت و جلوگیری از خوردگی آن ها را
تشدید می کند، گالوانیزه گرم می گویند؛ در صورتی که اگر برای پوشش فلزات تنها از
آبکاری استفاده شود فرایند الکترو گالوانیزاسیون یا گالوانیزه سرد انجام شده است.
حال با بررسی تفاوت های اصلی این فلزات درک بهتری از خرید هر کدام خواهید داشت:
1-تولید
اولین تفاوت این دو
محصول در روش تولید آن ها است که در ادامه به صورت کامل شرح داده شده است. در این
مورد می توان گفت ورق گالوانیزه گرم از طریق غوطه ور شدن فولاد در حوضچه های مذاب
حاوی فلز روی به دست می آید؛ در صورتی که گالوانیزه سرد به وسیله عملیات آبکاری
انجام شده و در آن از یک جریان الکتریسیته در یک محلول نمکی شامل آند روی و کاتد
فولادی استفاده می کنند تا پوشش بر سطح محصول اعمال شود.
در واقع باید گفت گالوانیزه
گرم با دمایی در حدود 450 درجه سانتی گراد انجام می گیرد، اما که گالوانیزه سرد در
دمای معمولی فضا صورت می گیرد. این تفاوت سبب ایجاد سایر تمایز ها میان ورق های
گرم و سرد گالوانیزه شده است. همچنین سرعت فرایند گالوانیزه سرد بیشتر بوده و با
حساسیت کمتری انجام می شود، اما در گالوانیزه گرم حساسیت های بسیاری باید مد نظر
قرار بگیرد تا محصول نهایی کیفیت مناسبی داشته باشد.
2-قیمت
دومین تفاوت گالوانیزه
گرم و سرد در قیمت آن ها است. استفاده از روش غوطه وری جهت تولید ورق گالوانیزه
توجیح اقتصادی داشته و در مقایسه با روش الکترو گالوانیزه، محصول نهایی قیمت مقرون
به صرفه تری دارد. قیمت ورق گالوانیزه در روش گالوانیزه سرد به سبب روش تولید راحت
تر، با سرعت بیشتر و ضخامت پوشش کمتر، مناسب تر می باشد، اما در عوض ورق گرم این
محصول از ویژگی های بهتری به خصوص برای استفاده طولانی مدت و همچنین خواص مکانیکی
برخوردار است.
به طوری که در گالوانیزه گرم عملیات هایی نظیر چربی زدایی، شستشو، آنیلینگ یا بازپخت، غوطه وری در حوضچه های مذاب، تست ضخامت پوشش و تنظیم آن و در نهایت پوشش دهی کروماته صورت می گیرد، اما گالوانیزه سرد در دمای معمولی فضا تنها شامل فرآیندهای چربی زدایی و اعمال پوشش روی به صورت ساده یا رنگی بر روی فولاد زیرین و در نهایت پوشش محافظ است. شما می توانید قیمت روز هر کدام از این فلزات را در صفحه جداول فولاد گالوانیزه وب سایت آهن اینفو مشاهده نمایید. با این حال پیشنهاد می شود ابتدا کاربرد نهایی خود را مشخص کنید تا بتوانید انتخاب درستی با توجه به تفاوت های میان این دو محصول داشته باشید.
حتما بخوانید:تفاوت ورق روغنی و گالوانیزه
3-شکل ظاهری
شکل
ظاهری شیت های گالوانیزه گرم به سبب اعمال شدن پوشش روی همزمان با حرارت، رنگی
خاکستری یا نقره ای تیره را به خود اختصاص داده است. البته این موضوع به علت رنگ
فلز روی نیز می باشد، اما این در صورتی است که ورق های گالوانیزه شده به روش محلول
روی نمکی یا سرد دارای سطحی بسیار روشن تر هستند. در واقع شکل ظاهری شیت های
گالوانیزه سرد بسیار شبیه به ورق های روغنی شفاف و صیقلی می باشد.
از
سوی دیگر ضخامت پوشش این فلزات بسیار کمتر بوده و به همین علت برای کاربردهای مهمی
که به فرم پذیری بالا احتیاج دارند (مانند تولید شیت های شیروانی)، از ورق های گرم
گالوانیزه استفاده می شود. این فلزات دارای انواع مختلف با طیف رنگی متفاوتی بوده و
همین موضوع سبب اهمیت قیمت ورق شیروانی رنگی برای مصرف کنندگان به خصوص برای پوشش
دهی انواع سقف ها شده است. به طور معمول از ورق های گرم برای ساخت این محصولات
استفاده می شود؛ زیرا لازم است که فولاد زیرین آن ها از استحکام و در عین حال انعطاف پذیری
متناسبی برای عملیات فرمینگ و عوامل مختلف برخوردار باشد.
4-ضخامت
چهارمین تفاوت مربوط به
تمایز در ضخامت آن ها می باشد. شیت های گالوانیزه سرد ضخامت پایین تری در مقایسه
با محصولات گالوانیزه گرم داشته و این موضوع به سبب روش تولید آن ها است. روش غوطه
وری سبب اعمال میزان بیشتری از پوشش روی بر سطح محصول می شود. سطح ظاهری آن ها نیز
مات، کدر و طوسی رنگ بوده؛ در صورتی که فلزات گالوانیزه سرد سطحی درخشان و صیقلی
دارند. با این وجود می توان گفت ضخامت ورق های گرم گالوانیزه در حدود 18/0 تا 4
میلی متر می باشد، اما ضخامت ورق های سرد بین 12/0 تا نهایت 5/1 میلی متر در نظر
گرفته می شود.
این موضوع سبب ایجاد
تمایز در کاربردهای این دو نیز به طور مجدد خواهد شد و باز می توان کاربری اصلی
این فلزات، یعنی تولید شیت های شیروانی ذوزنقه، کرکره، سینوسی و ... را مثال زد.
از این رو برای خرید ورق شیروانی بهتر است بدانید این فلزات از طریق گالوانیزه های
گرم ساخته شده و به همین علت استحکام و در نهایت طول عمر متناسبی برای پوشش سقف،
حصار دور زمین، سوله سازی و ... را به خود اختصاص می دهند.
5-سطح
در
فرآیند گالوانیزه گرم، پوشش روی به وسیله حوضچه های مخصوص بر سطح و زیر فولادها
قرار می گیرد، اما اعمال این پوشش با غلظت مناسبی صورت گرفته و همچنین سرد شدن آن
با روش های مخصوص و سرعت مشخصی انجام می گیرد. در زمان سرد شدن پوشش روی بر سطح
ورق گالوانیزه گرم، یک سری عیوب با طرح های جالب بر سطح این محصولات به وجود می
آید که به اسپانگل یا گل گالوانیزه شهرت دارند. این در صورتی است که گالوانیزه های
سرد دارای سطحی بسیار صاف تر، صیقلی تر و بدون طرح و تخلخلی هستند.
در
واقع ورق های گالوانیزه به سه صورت بدون گل، گل ریز و گل درشت در بازار عرضه می
شوند و این موضوع سبب شده تا نحوه تشخیص آن ها نسبت به ورق های روغنی یا اسیدشویی
راحت باشد. البته قیمت ورق روغنی معمولاً مقرون به صرفه تر از ورق گالوانیزه می
باشد؛ زیرا این محصول ماده اولیه فولاد گالوانیزه به شمار می آید و فرآیند کمتری
برای تولید آن (اسیدشویی شیت های گرم و در نهایت عملیات های نورد سرد) نیاز است.
6-خواص شیمیایی
منظور
از خواص شیمیایی، مشخصاتی است که به سبب ترکیبات پوشش روی بر روی شیت های
گالوانیزه گرم و سرد به وجود می آید. در این مورد باید گفت ورق های گرم و سرد هر
دو دارای استحکام و مقاومت کافی در برابر خوردگی، زنگ زدگی، اکسیداسیون و خوردگی
می باشند، اما این موضوع بسته به ضخامت پوشش روی متفاوت است.
همچنین
این که شیت های گالوانیزه سرد به سبب روش تولید با ضخامت پوشش کمتر و در نتیجه سطح
صاف تر و یکنواخت تری به دست می آیند، درست است، اما از سوی دیگر ورق های گرم
دارای استحکام بالاتری به سبب ضخامت پوشش بیشتر در برابر عوامل ذکر شده می باشند.
از
این رو محبوبیت ورق های گالوانیزه گرم به خصوص نسبت به گالوانیزه سرد، شیت های
سیاه یا روغنی در چندین سال اخیر افزایش پیدا کرده است. البته این موضوع در مقایسه
قیمت آن ها اثرگذار بوده و به همین علت قیمت ورق سیاه مناسب تر از شیت های گالوانیزه
یا روغنی می باشد؛ زیرا ورق های سیاه از جمله ابتدایی ترین محصولات تخت فولادی می
باشند که از تولید آن ها سایر ورق های فولادی سرد و پوششی به دست می آیند.
7-کاربرد
در
نهایت باید گفت این تفاوت ها سبب تمایز در کاربرد و ویژگی های نهایی آن ها خواهد
شد. محصولات گالوانیزه گرم مقاومت بهتری در برابر خوردگی و زنگ زدگی داشته و از آن
ها در ساخت دکل های مخابراتی، بدنه لوازم خانگی مانند یخچال، فریزر، لباسشویی،
سینی پشت اجاق گاز، بدنه و شاسی خودروها، کانال کولر و تهویه، بدنه رایانه ها، تجهیزات
گرمایشی و سرمایشی مانند لوله بخاری، ساخت رادیاتور، مخازن و تانکرهای حمل آب،
تجهیزات الکترونیکی، ساخت ساندویچ پانل، تولید ورق های شیروانی، لوله های آب، دکل
های فشار قوی و برخی از تیرهای برق استفاده می کنند.
کاربرد محصولات سرد نیز به علت داشتن مقاومت کمتر در مقایسه با شیت های گالوانیزه گرم در مواردی بهتر پاسخ می دهد که به مقاومت کمتری در برابر عوامل ذکر شده، نیاز باشد. بیشترین استفاده از آن ها در ساخت محصولات بهداشتی، ساخت قطعات خودرو، پیچ و مهره و ساخت لوله های با ضخامت پایین می باشد.
حتما بخوانید:تفاوت ورق سیاه و گالوانیزه
8-عمر و ماندگاری
در روش غوطه وری یک
واکنش شیمیایی مابین فولاد و فلز روی به وجود می آید که سبب تثبیت چسبندگی پوشش
روی شده و در صورت ایجاد خراش به راحتی از بین نمی رود. در صورتی که روش الکترو
گالوانیزه این واکنش را نداشته و پوشش آن راحت تر از بین می رود. همین تفاوت سبب
ایجاد تمایز در طول عمر این دو محصول نیز خواهد شد. فلزات تولید شده در روش اول به
علت چسبندگی بالای پوشش روی، طول عمر بیشتری در مقایسه با فلزات سرد دارند.
در نهایت باید گفت طول عمر شیت های گرم گالوانیزه در حدود 20 تا 30 سال بوده و طول عمر ورق های سرد این دسته بندی تا حدود 10 سال است. این موضوع نیز به ضخامت پوشش روی ورق گرم باز می گردد که در روش غوطه وری گرم بسته به کارخانه تولیدکننده بین 90 تا 275 گرم بر متر مکعب در نظر گرفته می شود.
گالوانیزه گرم چیست
گالوانیزه
گرم در واقع عملیاتی است که طی آن ورق های سرد یا روغنی را برای گالوانیزه شدن در
حوضچه های مذاب حاوی فلز روی غوطه ور می کنند. دمای این حوضچه ها در حدود 460 درجه
سانتی گراد بوده و به همین علت فرآیند حاصل گالوانیزه گرم نامیده می شود. در این
عملیات پوشش روی با جرم بیشتری بر سطح شیت های فولادی قرار گرفته و در نتیجه
استحکام و مقاومت بالاتری را برای محصولات نهایی به وجود می آورد.
همچنین
در طی این فرآیند برای تنظیم پوشش روی بر سطح ورق ها، به علت آبکاری گرم و سرد شدن
آن یک سری طرح با نام اسپنگل یا گل گالوانیزه بر سطح شیت ها به وجود خواهد آمد. از
این رو ورق های حاصل از گالوانیزه گرم در سه نوع گالوانیزه گل ریز، گل متوسط و گل
درشت به فروش می رسند. همچنین در برخی مواقع به سبب تغییر در استانداردهای تولید و
سرد شدن پوشش، گالوانیزه بدون گل نیز تولید می شود.
گالوانیزه سرد چیست
گالوانیزه
سرد یکی دیگر از روش های تولید ورق گالوانیزه به شمار می آید که در آن دمای بالایی
وجود ندارد و بر پایه عملیات هایی نظیر آبکاری یا الکترولیز با استفاده از محلول
نمکی و جریان برق می تواند صورت گیرد. این فرآیند قادر است یک پوشش بسیار صاف و
صیقلی را بر سطح ورق های فولادی مد نظر ایجاد نماید که ضخامت آن نیز کاملاً قابل
تنظیم است. البته بهتر است بدانید با کاهش جرم پوشش روی، مقاومت و استحکام نهایی
محصول نیز کاهش پیدا می کند.
به طور معمول محصولات حاصل از فرآیند گالوانیزه سرد برای مصارفی مورد استفاده قرار می گیرند که زیبایی و سطح مناسب مد نظر باشد. با این وجود می توان در این عملیات از یک رنگ غنی از روی در سطح ورق ها نیز جهت زیباسازی بیشتر استفاده کرد و این موضوع نیز به افزایش مقاومت ورق های گالوانیزه سرد تا حدودی کمک می کند.
جمع بندی
در این مطلب به بررسی تفاوت های میان ورق های گالوانیزه گرم و سرد پرداختیم که اصلی ترین تمایز آن ها در روش تولید می باشد. در واقع روش تولید حتی اگر توسط کارخانجات به یک شکل و مطابق با یک استاندارد انجام شود، در نهایت غلظت محلول روی، دمای حوضچه ها و روش سرد کردن پوشش است که کیفیت نهایی ورق گالوانیزه را تعیین می کند. قابلیت هایی از جمله رنگ پذیری، جوش پذیری و فرم پذیری و البته مقاومت در برابر خوردگی و زنگ زدگی باید در تمامی محصولات نهایی حاصل از این دو روش وجود داشته باشند، اما میزان آن ها با یک دیگر متفاوت است.