بررسی فرآیند احیا مستقیم در تولید فولاد
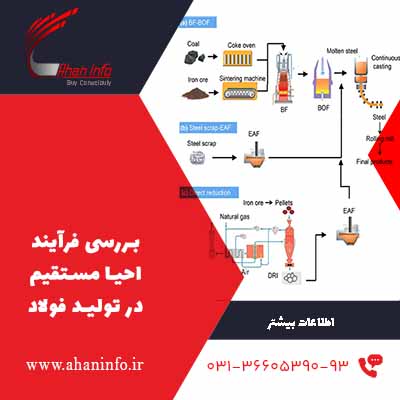
امروزه صنعت فولاد یکی از مهم ترین صنایع در کل جهان به شمار می آید. بر اساس برخی از گزارشات مصرف سرانه این ماده به عنوان یک شاخص برای ارزیابی صنعتی بودن یک کشور شناخته می شود. در کشور ما نیز تولید و مصرف فولاد در واحد های فولادسازی و صنعتی در بهترین حالت خود قرار داشته و بخش زیادی از صنایع را پوشش می دهد. یکی از مدرن ترین روش های دنیا برای تولید این ماده فرآیند احیا مستقیم است که در این مطلب قصد بررسی آن را داریم.
محصولات و مقاطع فولادی
با داشتن خواص و ویژگی های مختلف، متناسب با هر صنعت در واحد های تولید کننده کشور
تولید می شوند و در این صنعت ها که برخی از وسایل آن ها در زندگی روزمره ما به کار
می روند، به کار برده می شوند. در نهایت این صنعت بر بسیاری از نوسانات اقتصادی و
سیاسی اثرگذار است.
جالب است بدانید اولین
اقدامات برای تأسیس و شروع فعالیت کارخانجات آهن و فولاد در کشور مربوط به قبل از
سال 1930 میلادی است که البته به علت مشکلات جنگ جهانی دوم نتیجه ای نداشت. با
گذشت زمان در پایان سال 1350 اولین کارخانه با نام ذوب آهن در اصفهان و ظرفیت 550
هزار تن مقاطع فولادی در سال فعالیت خود را آغاز کرد.
پس از گذشت دو دهه از
تمام شدن جنگ جهانی دوم، دو عامل سبب تأسیس کارخانه ذوب آهن اصفهان شدند که شامل
بهبود وضعیت اقتصادی کشور و افزایش تقاضای داخلی فولاد بودند. در کارخانجات تولید
کننده محصولات فولادی، معمولاً یک واحد نورد برای فولادهای ساختمانی وجود دارد که
با واردات محصولات نیمه نهایی فولادی و انجام عملیات نورد، سایر مقاطع به بازار
این صنعت عرضه می شوند. به طور کلی برای تولید فولاد دو روش در دنیا وجود دارد:
- بر اساس سنگ معدن Mill Integrated Base-Ore :
این روش با استفاده از سنگ آهن استخراج شده از معادن این ماده انجام می گیرد. با
فراوری و احیا مستقیم سنگ آهن به دست آمده از معادن، اکسید آهن احیا شده و آهن خام
بعه دست می آید. سپس طی عملیات های مختلف در واحد فولاد سازی و همچنین افزودن یک
سری عناصر (مانند کربن)، فولاد مذاب به دست می آید.
- بر اساس قراضه: در این روش با استفاده از ذوب آهن
و فولاد و قراضه های آن ها در کوره های قوس الکتریکی، ناخالصی های مواد حذف شده و
با افزودن عناصر دیگر فولاد تولید می گردد.
فرآیند احیا مستقیم چیست؟
فرآیند احیا مستقیم یکی
از اصلی ترین روش ها برای تولید فولاد است. فولاد یکی از اصلی ترین آلیاژهای آهن
است که خود انواع مختلفی دارد، اما کاربرد بسیار زیادی در صنعت داشته و هر محصول
با داشتن روند تولید و استاندارد های متفاوت، ویژگی های اختصاصی برای خود دارد. از
این رو کاربرد محصولات و قطعات فولادی با یک دیگر متفاوت است.
کیفیت فرآیند احیا
مستقیم است که تعیین کننده محصول نهایی فولادی خواهد شد. در فرآیند احیا مستقیم
گاز طبیعی یا احیا دهنده که از طریق شکستن گاز متان در گازشکن ها به دست می آید،
مورد استفاده قرار می گیرد. خوشبختانه کشور ما از منابع گاز طبیعی غنی بوده و از
این نظر مشکلی ایجاد نمی شود. در دنیا حدود 7 درصد از فولاد خام تولیدی به وسیله
این روش به دست می آید.
احیا مستقیم یک روش جدید
برای تولید آهن خالص، البته با عیار بالا به شمار می آید؛ در نتیجه می توان گفت
کیفیت این فرآیند تأثیر بسیار زیادی بر روی قیمت آهن آلات دارد؛ زیرا روش های
مختلفی داشته و هر تولید کننده با به کارگیری هر روش سبب تولید کیفیت متفاوتی از
فولاد می شود. علت این موضوع برای ناخالصی هایی است که در سنگ آهن وجود داشته و
برای از بین بردن آن ها عملیات های مختلف احیا انجام می گیرد. آهن خالصی که از این
فرآیند به دست می آید دارای عیار 90 درصد می باشد. لازم به ذکر است کانی های داخل
سنگ آهن که شامل مگنتیت، هماتیت و وستیت هستند با مواد افزودنی توسط این فرآیند
ترکیب شده تا ناخالصی ها از بین برود و آهن خام به دست آید.
مراحل احیا مستقیم فولاد
احیا مستقیم فولاد طی
چهار مرحله زیر انجام می گیرد:
گندله سازی
گندله با اسامی مختلفی
مانند کنسانتره یا سنگ آهن خرد شده شناخته می شود. در واقع برای فراوری ابتدا باید
سنگ آهن به گلوله های کوچک 8 تا 16 میلی متری تبدیل شود. در تولید گندله ابتدا سنگ
آهن در معرض حرارت قرار گرفته و خرد می شوند. گندله ها گوی های متخلخل کوچکی هستند
که ابتدا به شکل کنسانتره هستند و سپس دانه های ریز و درشت آن ها جدا می شود. در
نهایت نیز با استفاده از دیسک های واحد به گندله تبدیل می شوند و سپس مجدداً در
کوره های پخت قرار می گیرد تا در پایان سرد و به واحد احیا منتقل شوند.
احیای مستقیم
احیا مستقیم معمولاً به
دو روش HYL و MIDREX
انجام می گیرد. البته روش های دیگری نیز وجود دارد که در ادامه شرح خواهیم داد،
اما در این دو روش به ترتیب از کوره های القایی و کوره های قوس الکتریکی استفاده
می کنند. در کشور ما نیز کوره های قوس الکتریکی یا روش میدرکس بیشتر کاربرد داشته؛
زیرا مزیت های بسیار زیادی دارد و با استفاده از گاز طبیعی و مونواکسید کربن انجام
می گیرد. سپس این دو ماده با اکسیژن موجود در گندله ها واکنش نشان داده و آنچه
آزاد می شود، هیدروژن است.
این دو ماده سبب آزاد
شدن بخار آب، حذف ناخالصی ها و در نتیجه تولید آهن با عیار بیشتر خواهند شد. این
ماده همان آهن اسفنجی است که پس از تولید در کوره های فولاد سازی به تختال و سپس
به ورق گرم یا آهن تبدیل می شود. با این وجود می توان گفت هزینه های فرآیند های
احیا و فولادسازی در قیمت ورق آهن یا هر محصولی که از فولاد مذاب به دست آید،
اثرگذار است. جالب است بدانید ورق سیاه یا آهن بیشترین کاربرد را به علت داشتن
آلیاژهای مختلف و کاربردی در صنعت به خود اختصاص می دهد و از این رو نرخ آن برای
مصرف کنندگان از اهمیت بسیاری برخوردار است.
روش هاي تولید آهن به روش احیا مستقیم
تکنولوژي کوره بلند : کنورتر Furnace
Blast
روش کوره بلند به وسیله
ماده احیا کننده ای به نام کک انجام می گیرد. کک با استفاده از زغال سنگ تولید شده
و در کوره های اکسیژنی (BOF) برای تولید فولاد با آهن ترکیب می شود. این
تکنولوژی مهم ترین روش تولید فولاد در جهان به شمار می آید و حدود 60 درصد از
فولاد خام جهان به وسیله این روش تولید می گردد.
بهتر است بدانید در کنار
فرآیندهای اصلی آهن سازی و فولادسازی، سایر عملیات های جانبی مانند کک سازی برای
آماده سازی ماده اولیه و عملیات احیا و آگلومراسیون برای آماده کردن سنگ آهن برای
ذوب در کوره انجام می گیرد. در این روش برای تبدیل این مواد به فولاد، از کوره های
اکسیژنی استفاده شده و در آن ها مواد اولیه به همراه قراضه آهن، چدن و ... به
وسیله اکسیژن با خلوص بالا به فولاد مورد نظر تبدیل می شوند. در واقع می توان گفت
نرخ مقاطع و ورق های فولادی وارداتی و صادراتی بر اساس این روش تعیین می شوند؛
زیرا بیشترین تولید فولاد خام جهان با استفاده از روش کوره بلند تولید می شود.
منظور از این محصولات همان ورق سیاه، روغنی، گالوانیزه و انواع میلگرد و نبشی و
... هستند که نرخ برخی از آن ها مانند قیمت ورق گالوانیزه به علت داشتن مقاومت در
برابر رطوبت، زنگ زدگی و خوردگی اهمیت بسیار زیادی برای خریداران دارد. از سایر
ویژگی هایی که سبب محبوبیت این قطعه می شود، می توان به فرم پذیری، جوش پذیری،
قابلیت رنگ آمیزی و سازگاری با انواع شرایط جوی اشاره کرد.
احیاء مستقیم : کوره هاي قوس الکتریکی (میدرکس)
دومین تکنولوژی تولید
فولاد احیا مستقیم به روش میدرکس نامیده می شود. برای استفاده از این روش نیاز به
منابع غنی از گاز طبیعی CH می باشد؛ به همین علت در کشور ما از این روش
استفاده می کنند. پس از کشف ذخایر بزرگ گاز طبیعی در کشور و احداث شبکه سراسری
انتقال گاز طبیعی و توسعه گرفتن روش احیا، تولید فولاد مذاب کشور ایران نیز با
استفاده از این روش مورد توجه قرار گرفت.
پیش از بررسی این فرآیند
می توان نتیجه گرفت نرخ محصولات فولادی بر اساس این روش مشخص می شود. به طور مثال
می توان به مهم ترین محصول فولادی در مقاطع تخت یعنی ورق سیاه اشاره کرد. این فلز
با داشتن خواص شیمیایی و فیزیکی مخصوص، مورد توجه بسیاری از صنایع مهم کشور مانند
مخزن سازی، لوله سازی، کشتی سازی و خودروسازی قرار گرفته است. در واقع می توان گفت
قیمت ورق سیاه در ساخت مخازن تحت فشار، لوله های انتقال، بدنه کشتی و تجهیزات
خودروها تأثیر بسیار زیادی دارد و این موضوع به علت تنوع در ترکیبات و در نتیجه
گریدهای حاصل از این محصول است.
در این روش از کوره های قوس الکتریکی و گاز احیا کننده استفاده می شود. گاز احیا کننده از شکستن گاز متان در گازشکن ها تولید شده و از پایین درون کوره دمیده می شود. مواد اولیه که شامل آهن اسفنجی، قراضه های آهن و مواد سرباره هستند از بالا در کوره ریخته می شوند و در همین حین به وسیله الکترود که از لوله های خنک کننده به مخلوط منتقل می شود، ناخالصی های مواد جدا شده و سپس گاز احیا کننده از بالا به همراه سرباره و مواد اضافی خارج می شود. در نهایت فولاد مذاب به دست آمده از جلو داخل پاتیل های حمل مذاب ریخته می شود تا به واحد ریخته گری منتقل گردد.
حتما بخوانید:بررسی میزان بازیافت فلزات به صورت کامل
روش HYL
نام روش HYL یا فرآیند احیا به وسیله کوره های القایی از
اولین کمپانی سازنده مکزیکی به نام HYSA
گرفته شده است. اولین واحد صنعتی نیز که تولید فولاد را با استفاده از کوره های
القایی انجام داد، در مکزیک و با ظرفیت 75 هزار تن ساخته شد. اساس روش HYL به وسیله گاز احیا کننده که از تغییر فرم گاز
طبیعی به دست آمده است، انجام می گیرد. تبدیل این گاز به بخار آب و استفاده از آن
در راکتور ساکن می باشد.
محصولات تولیدی در این
روش از نظر ظرفیتی بیشتر هستند. در برخی موارد که صنایع مهم نیاز به ورق های مخصوص
ساخت مخازن تحت فشار به مقدار زیاد دارند، نیاز به یک روش احیا با ظرفیت بالا می
باشد. کوره های القایی با داشتن حوضچه هایی در زیر خود، ظرفیت تولید فولاد بیشتری
را دارند. محصول مورد نیاز برای ساخت مخازن تحت فشار ورق سیاه با گرید ST52 است. البته بهتر است بدانید قیمت ورق ST52 علاوه بر این صنعت به علت داشتن وزن سبک و مقاومت بالا در صنایعی مانند
خودروسازی، پل سازی و سد سازی تأثیر به سزایی دارد. البته تمامی این موارد بسته به
کارخانه فولادسازی و میزان ظرفیت و تعداد کوره های آن متفاوت است.
روش پروفر
پروفر نام یک کمپانی
آلمانی است که روش هایی را در جهت تولید آهن ارائه می کند. البته روش پروفر چندان
مورد استقبال قرار نگرفت و به همین دلیل تنها کمتر از 10 درصد فولاد جهان با این
روش تولید می شود.
احیاء مستقیم به روش
پرد
PERED
یکی دیگر از فرآیندهای
تولید فولاد، پرد نام دارد که در آن گندله های اکسید آهن به آهن اسفنجی تبدیل می
شود تا برای فولادسازی با کیفیت بالا آماده شود. در این روش از یک کوره احیا با
شکل استوانه ای و یک جریان پیوسته با بازدهی بالا استفاده می کنند. اکسید آهن از
مخزن تغذیه کوره احیا با استفاده از نیروی جاذبه و یک لوله عایق شده توسط گاز آب
بندی، به لوله های توزیع کننده و سپس کوره احیا شارژ می شود.
در کوره احیا آهن اسفنجی
تحت نیروی وزن و به وسیله فیدر ارتعاشی به پایین رفته و با استفاده از تماس مستقیم
با جریان مخالف گاز های احیا کننده در آن منطقه به آهن خام تبدیل می شود. به طور
کلی کوره استوانه اي به سه منطقه با سیستم گاز مجزا تقسیم می گردد:
- منطقه بالایی براي احیاء
- منطقه انتقالی براي کربن دهی
- منطقه پایینی براي خنک کردن
جمع بندی
در نهایت باید گفت
امروزه آهن و فولاد به عنوان دو عضو اصلی تمامی صنایع به شمار می آیند و کاربردهای
بسیاری را تحت مواد اولیه و ثانویه به خود اختصاص می دهند. با این وجود تولید هر
کدام به خصوص محصولات فولادی به راحتی نمی باشد و نیاز به مواد اولیه مانند سنگ
آهن یا قراضه ها و ضایعات آهنی به دست آمده از محصولات پیشین است. با این وجود این
مواد دارای ناخالصی های بسیاری هستند و برای تولید فولاد با کیفیت باید آن ها را جدا
و حذف کرد.
یکی از بهترین روش ها
برای فراوری سنگ آهن، استفاده از روش احیا مستقیم می باشد. این فرآیند به چندین
روش قابلیت انجام دارد و هر کشور بسته به بهره مندی خود از منابع طبیعی و غیر
طبیعی مختلف، از یک روش استفاده می کند. به طور مثال در روش میدرکس از گاز طبیعی
احیا شده استفاده می کنند. گاز احیا کننده از شکستن گاز متان در گاز شکن ها تولید
می شود. از سوی دیگر تمامی فرآیند ها مراحل گندله سازی و احیا مستقیم را در خود
دارند.
همان طور که در مطلب نیز
اشاره شد، امروزه حدود 60 درصد از فولاد جهان به روش کوره بلند تولید می شود، اما
در کشور ما به علت غنی بودن از منابع گاز طبیعی از روش میدرکس استفاده می گردد.
این روش شامل استفاده از کوره های قوس الکتریکی و الکترودها بوده که سبب اعمال
جریان به مواد قراضه به همراه آهن اسفنجی شده تا ناخالصی های آن ها جدا گردد. جدا
شدن ناخالصی ها و مواد سرباره که از بالا خارج می شوند، تولید فولاد مذاب را به
همراه دارد که در پاتیل های حمل مذاب از پایین کوره ریخته می شوند. به همین دلیل این
روش به علت داشتن صرفه اقتصادی و آسیب های زیست محیطی کمتر، در کشور ما رایج تر از
سایر روش ها می باشد.